In the manufacturing industry, every inch of material matters. Waste not only impacts production costs…
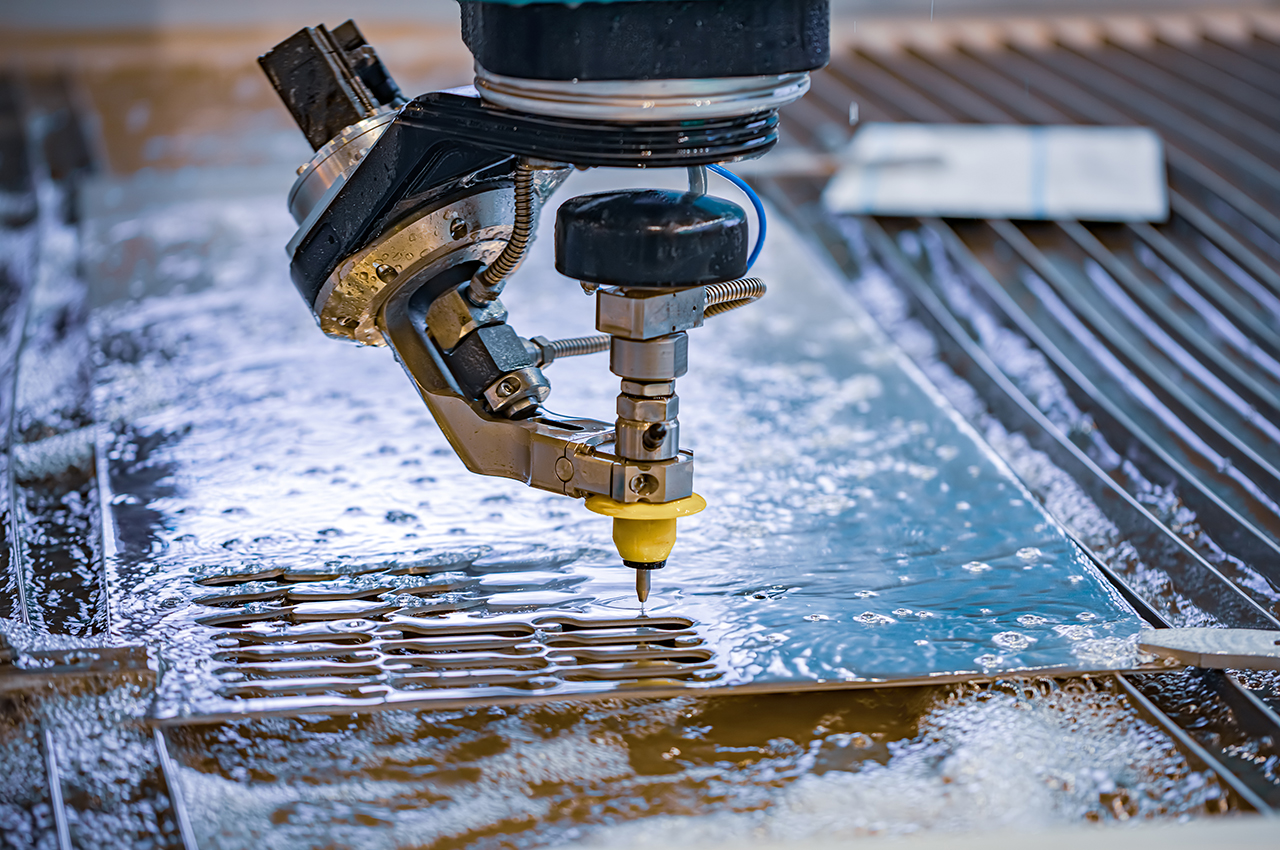
Innovation in the Industry: Waterjet and Laser Cutting for Stainless Steel
Stainless steel is one of the most versatile and essential materials in modern industry, used across a wide range of applications. Its corrosion resistance and durability make it ideal for manufacturing high-quality products. In this article, we’ll explore not only the history of stainless steel, its types, and uses but also how advanced cutting methods, such as waterjet and laser cutting, have revolutionized the way this material is processed in the industry.
History of Stainless Steel
The development of stainless steel began in the early 20th century when Harry Brearley, a British metallurgist, created a steel alloy with chromium in 1913. This innovation marked a milestone in corrosion resistance, laying the groundwork for what we know today as stainless steel.
Over the years, the popularity of this material surged, especially during World War II, when it was used in military applications. Today, stainless steel remains crucial in various industries, from construction to kitchenware manufacturing.
Top Stainless Steel Producing Countries
- China: The world’s largest stainless steel producer.
- Japan: A leader in producing high-quality stainless steel.
- Germany: Known for producing stainless steel with significant value for industrial applications.
- Italy: Famous for stainless steel products used in kitchenware.
- United States: Important in the production and export of stainless steel.
Types of Stainless Steel
There are various types of stainless steel, classified based on their chemical composition and properties:
- Austenitic: The most common, used in architectural structures and kitchen equipment.
- Ferritic: Corrosion-resistant, used in appliances and automotive applications.
- Martensitic: Known for its hardness, employed in cutting tools.
- Duplex: Ideal for chemical and marine applications.
- Precipitation-Hardened: Used in the aerospace industry for its extreme strength.
Innovation in Stainless Steel Cutting
Today, waterjet and laser cutting methods have transformed the way stainless steel is processed. Both methods offer unmatched precision, enabling industries to achieve finer and more detailed cuts, optimizing material use.
Waterjet Cutting
Waterjet cutting, also known as a waterjet, uses a high-pressure jet of water mixed with abrasives to cut hard materials like stainless steel. Some of its advantages include:
- Heat-free Cutting: Prevents distortion of the steel.
- Versatility: Can cut steel of varying thicknesses.
- Precision: Allows for detailed cuts without damaging the material’s structure.
This method is ideal for applications that require preserving the steel’s properties, such as in the aerospace industry or for custom parts manufacturing.
Laser Cutting
Laser cutting uses a high-intensity laser beam to cut stainless steel with great precision. Some of its advantages include:
- Speed: One of the fastest methods for cutting stainless steel.
- Fine Cuts: Perfect for intricate and complex details.
- Quality: Produces smooth edges without needing additional finishing processes.
Laser cutting is widely used in the automotive, electronics, and custom parts industries, where millimeter precision is essential.
Applications of Stainless Steel
Stainless steel has a variety of applications, many of which now benefit from advanced cutting techniques:
- Food Industry: Utensils and food processing equipment.
- Construction and Architecture: Building structures and facades.
- Chemical Industry: Corrosion-resistant tanks and pipelines.
- Appliances: Refrigerators, stoves, and more.
- Automotive: Exhaust system components and body parts.
- Medical and Healthcare: Surgical instruments and medical equipment.
The combination of stainless steel and advanced cutting techniques like waterjet and laser cutting has transformed how industries work with this material. These methods not only improve product precision and quality but also optimize the use of stainless steel, ensuring that this material remains essential in developing new technologies and applications.